How we working
How Is Magic Works
Crafting Quality Furniture: A Step-by-Step Guide to the Art of Woodworking
1
WOOD SELECTION
The primary step in the furniture manufacturing process is the selection of material. Its nature should depend on the piece of furniture you intended to produce with it. For instance, heavy furniture like wooden tables and bedframes require tough, durable materials like hardwoods (mahogany, teak, oak, etc.). They can endure daily use, support weight, and be waxed and polished to maintain their colour and smooth finish for years. On the other hand, if you want to make decor like kitchen cabinets, supporting beams, window frames and outdoor decks, then softwoods such as fir, ash or birch would do.
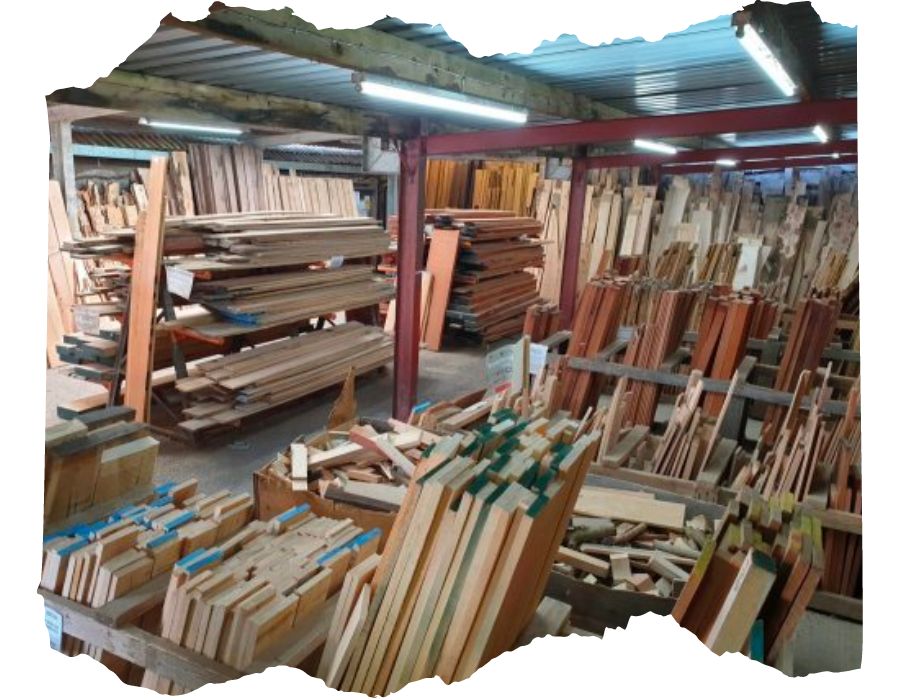
2
WOOD TRANSFORMATION
This is when the tree is cut into manageable beams and planks, called lumber (North America) or timber (elsewhere). These pieces are the raw material that get sawn and made into wooden furniture. The lumber is kiln-dried, so that the wood achieves its equilibrium moisture content (EMC), and does not gain or lose moisture because of its environment. At the same time, it retains the essential properties of wood. This transformation process is carried out at the sawmill, and its entirety can take about 2 to 4 weeks.
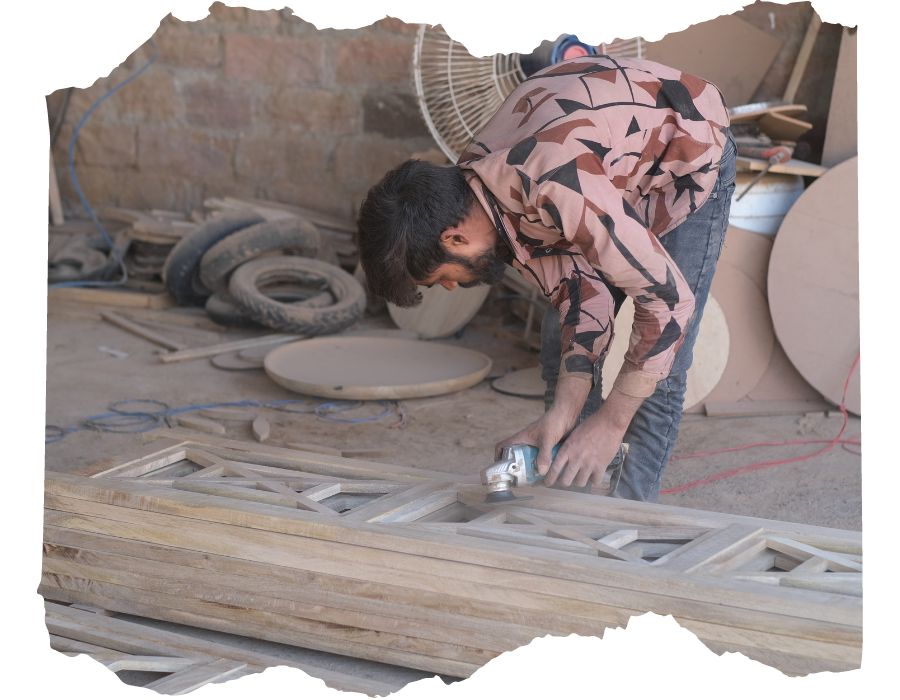
3
WOOD SPLITTING AND FINISHING
The kiln-dried wood is then passed to a machine shop, where it is sawed, planed, moulded and grooved as required. The different parts are cut out and clamped together and then brought in contact with a high-speed rotating knife that shapes each part to its proper size. The pieces are rough-carved on high-speed knives to be machine sanded, and finished by a hand carver later.
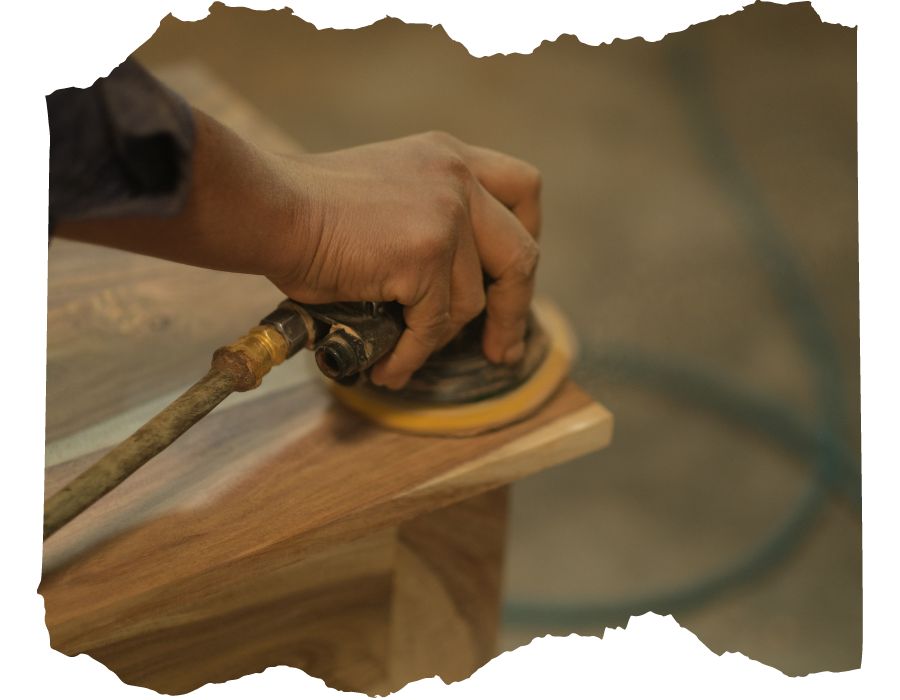
4
ASSEMBLY AND QULITY CHECK.
This is the step where the wooden carcasses (basic frameworks) are assembled, drawers are glued up, and doorframes are put together. Once the glue sets in and clamps are applied, the piece is sent to the machine department for machining that could not be performed before assembly. This includes sanding the joints and shaping the edges. Once this is complete, it is returned to the assembly department for the final structuring, wherein the piece is cleaned to remove excess glue. Hand sanding is done where required, followed by staining, spray polishing and treatments if any.
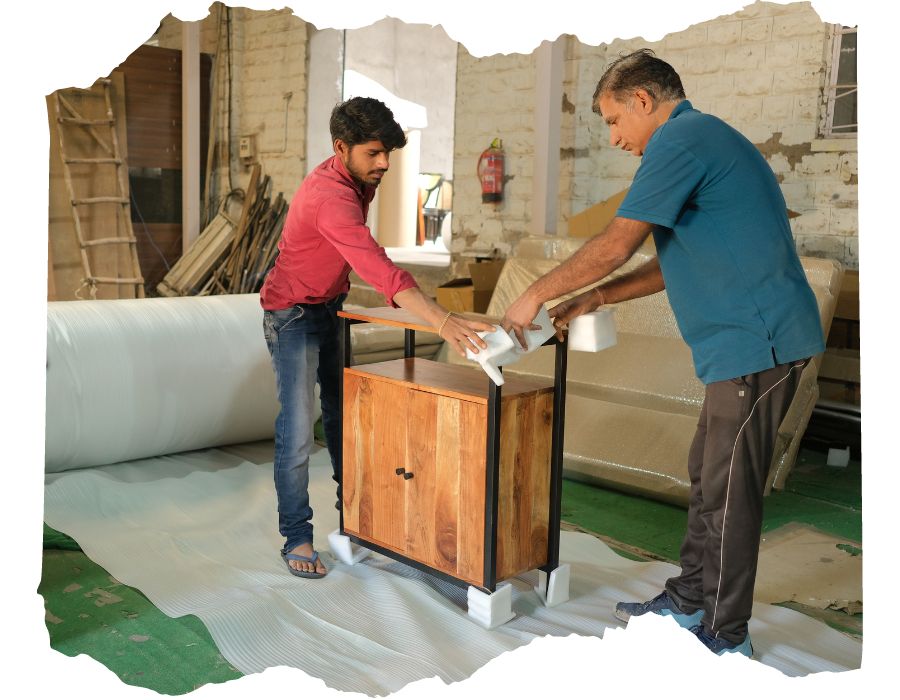
5
PACKAGING AND CONTAINER STUFFING
After approval from our or authorized third-party quality checkers, the products are readied for exports. During the packing process, we Keep environmental impact in mind during material disposal plus pollution laws of various countries. Our packing team uses various sustainable materials like recyclable PPE products and recycled cartons. At JIVAN, we use minimal but highly durable packing materials. Our packaging can sustain some of the toughest logistics conditions’, ensuring the product reaches in impeccable condition to the end customer. By having the consignment container stuffed in our factories, we ensure the goods reach the buyer’s warehouse in perfect condition by properly stuffing the container in house. This reduces the number of transfer points compared to stuffing in an ICD.
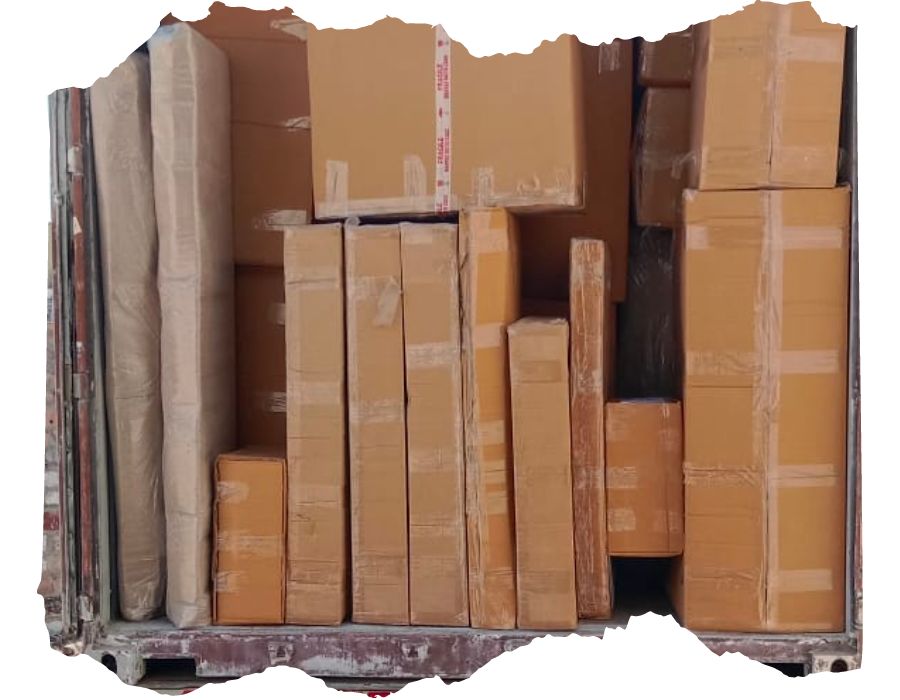